Bugatti demuestra de qué son capaces sus pinzas de freno impresas en 3D
www.diariomotor.com : ( )
Bugatti se ha puesto manos a la obra para reducir el peso de sus coches, por ello está trabajando con la impresión 3D para crear las mejores pinzas de freno jamás fabricadas. Destinadas al futuro uso por parte del Bugatti Chiron o el Bugatti Divo, estas pinzas de freno están fabricadas en titanio usando una impresora 3D, una revoluicionara técnica que hoy Bugatti nos muestra en vídeo que es capaz de conseguir resultados increíbles para domar los 1.500 CV del Chiron.
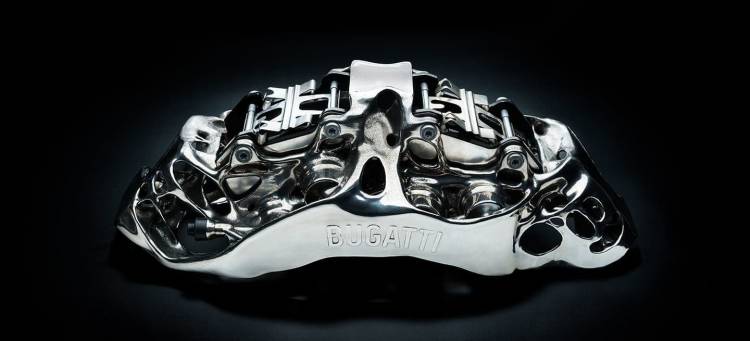
Los ingenieros de Bugatti quieren liderar el uso de la impresión 3D en titanio y por ello cuentan con la impresora más grande jamás fabricada para este material. El primer proyecto de Bugatti ha sido la creación de un componente de elevada complejidad por sus exigencias en tanto a diseño, resistencia, tolerancia, etc. Hablamos de pinzas de freno, un componente crucial en cualquier coche, pero que en el caso del Bugatti Chiron debe ser capaz de domar la friolera de 1.500 CV y velocidades por encima de los 400 Km/h.
La impresora 3D de Titano empleado por Bugatti es similar a la que por ejemplo ha empleado HRE para fabricar sus revolucionarias llantas en titanio por impresión 3D. Para crear las nuevas pinzas de freno se necesitan de 45 horas de trabajo, superponiendo nada menos que 2.213 capas de polvo de titanio. El resultado de este trabajo es un nuevo diseño de pinza de freno de gran resistencia, pero a la vez con una importante reducción de peso, de los 4,9 Kg que pesan las actuales pinzas del Chiron a 2,9 Kg de las nuevas pinzas impresas en 3D.
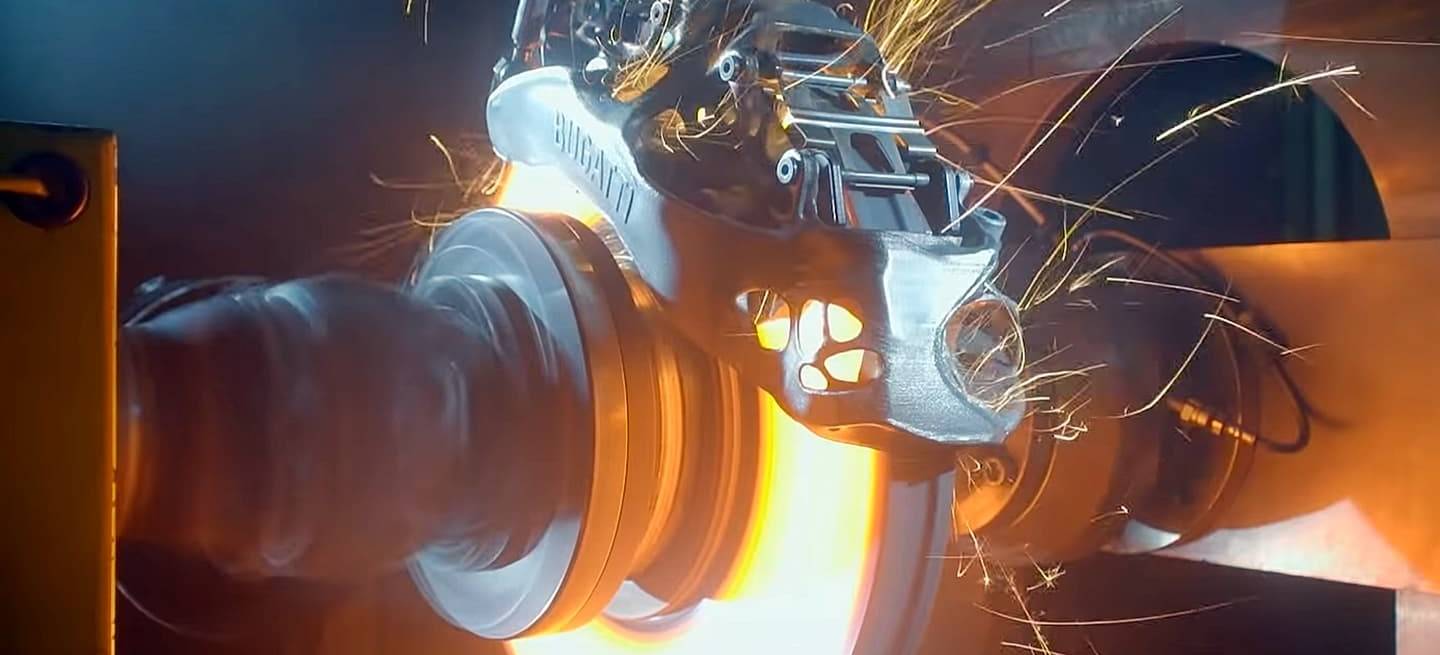
En este vídeo que acompañamos, Bugatti nos explica y muestra los test a los que está sometiendo al nuevo diseño de pinza de freno. Hemos de tener en cuenta que hablamos de un diseño aún en fase experimental, pero que Bugatti quiere llevar a las calles en cuanto sea posible. Los test de estrés que simulan este banco se basan en la continua repetición de aceleraciones hasta más allá de los 400 Km/h para después aplicar la máxima fuerza de frenado hasta lo que supondría una detención total. Así una y otra vez…